
Interference Fitted Assembly Tool
Assembly method and system, enabling interference-fitting of structural aero components.
Introduction
Within a gas turbine engine the HP-IP Strut Ring assembly is subject to demanding engine loads (thermal and stress) and is manufactured using nickel-based alloys. The struts are forged separately, cryogenically-frozen and inserted into the strut ring.
This is an extremely delicate operation, which must be performed fast and perfectly first time; the component must be placed correctly before it expands to prevent it from permanently locking into the wrong place.
MetLase was asked to design and build a fixture which would allow swift and precise insertion of this type of component.
Solution
MetLase developed a 2 part insertion assembly, comprising an alignment guide which locks over the disk, and a carrier for the strut, which goes into the liquid nitrogen bath.
Following customer input, the fixture was rapidly iterated to produce a final product which could be mounted to the assembly.
Ingenious flexure bearings were developed to ensure that the frozen component, once inserted, could swiftly be located in the housing at an angle with a precision of better than ±0.5 degrees from optimal.
Benefits
Rapid design and manufacture resulted in a delivery time of less than two months. The increase in accuracy and reduction in waste of this assembly created significant cost avoidance and can be rolled out on a series of engine variants.
Summary
Cost: Insertion fixture using ingenious “flexure bearings” developed to control strut angle to better than ± 0.5 degrees.
Fast Make: Rapid design and manufacture improved delivery by 2 months.
Solution: Optimised to the customer’s requirement via rapid design iteration.
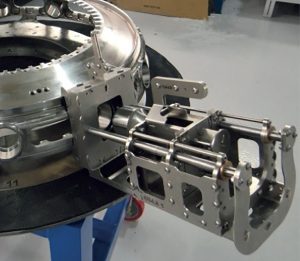
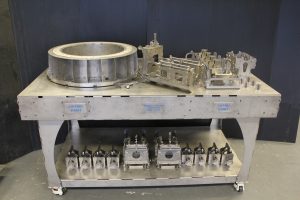
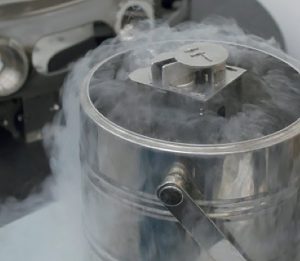


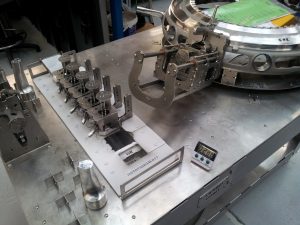